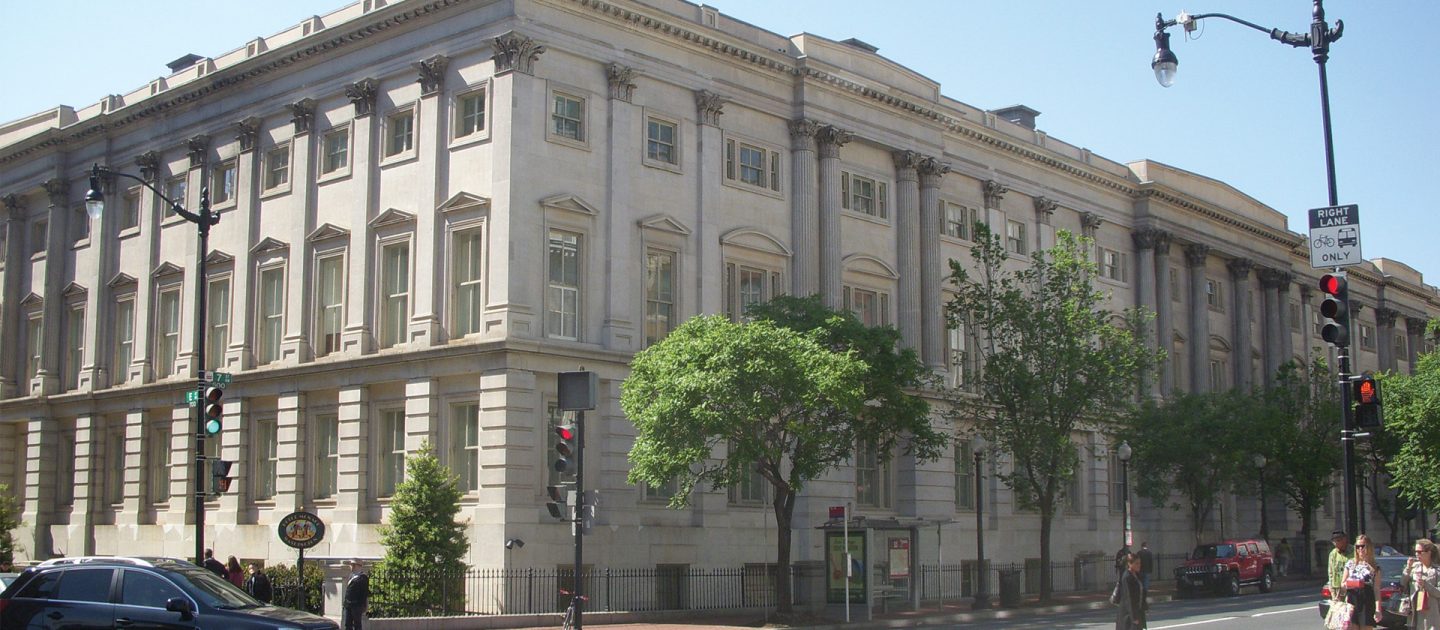
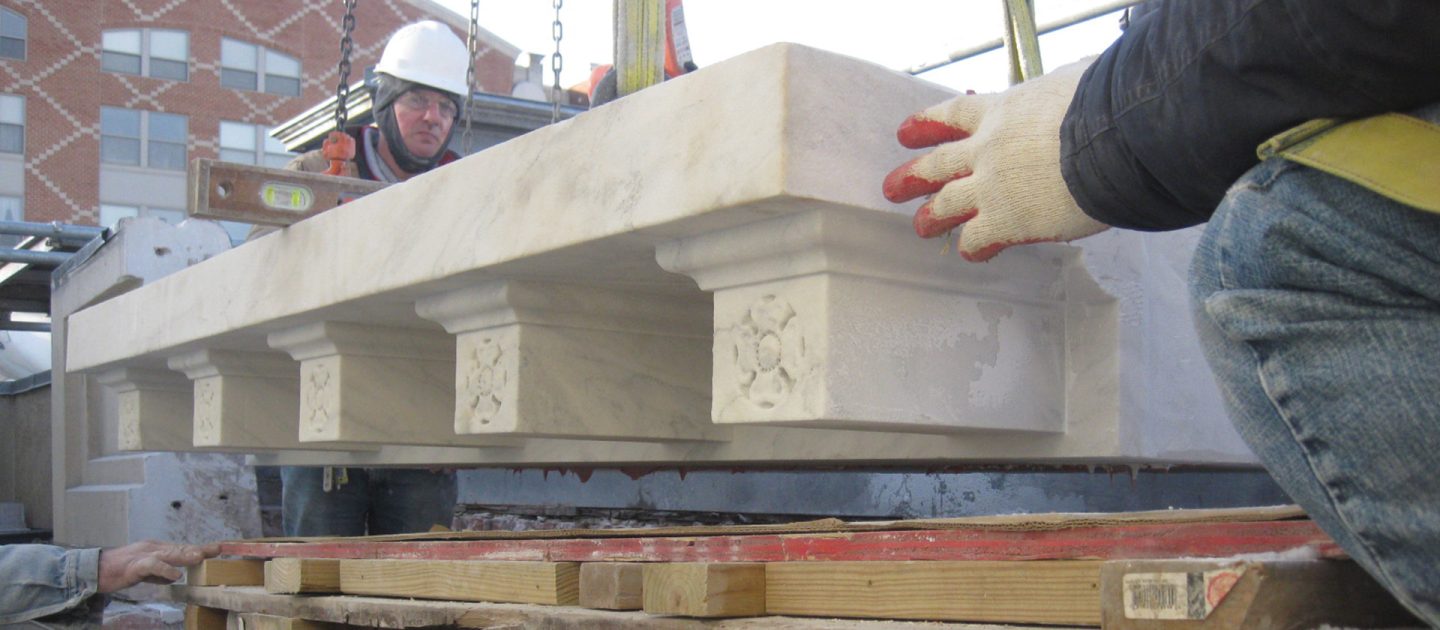
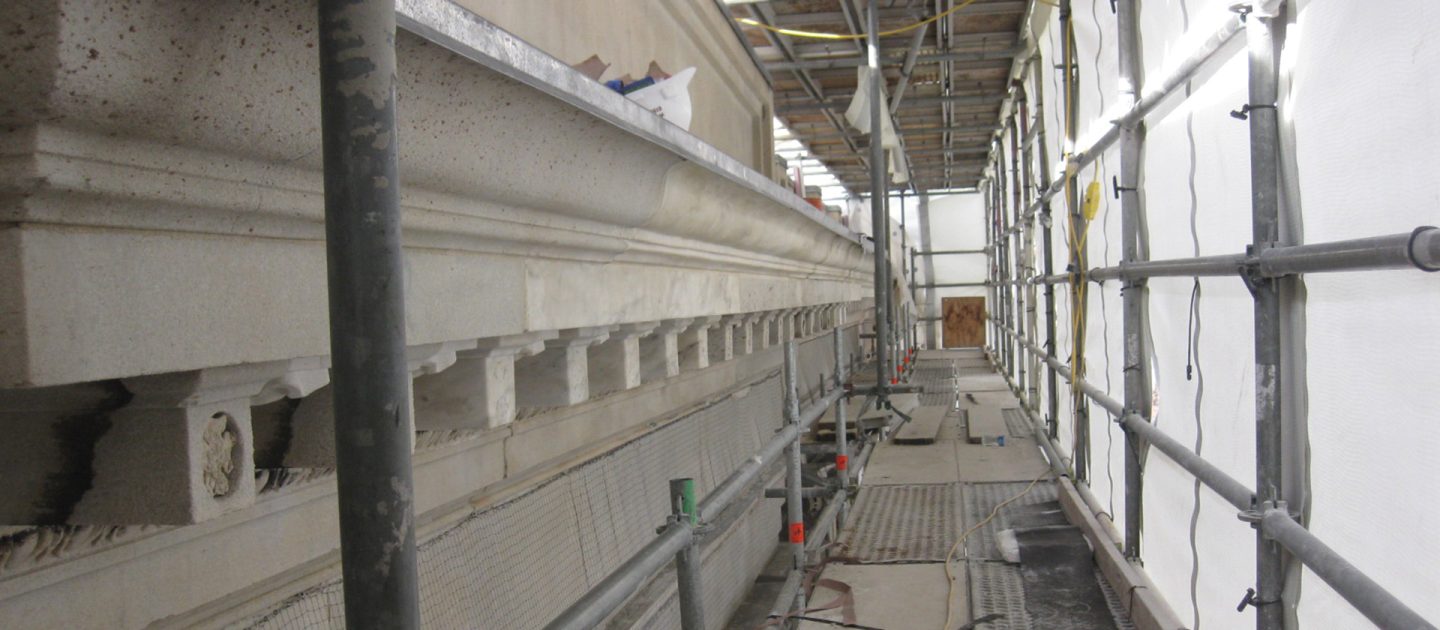
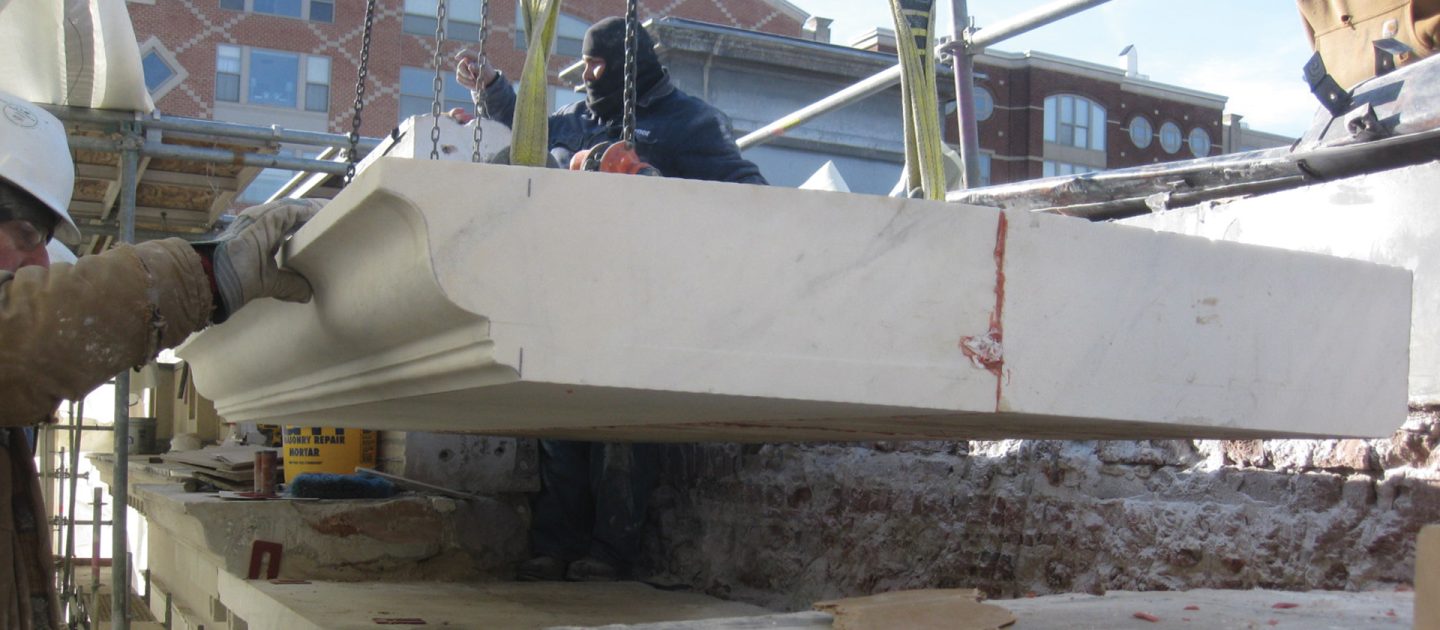
Hotel Monaco
Historic Cornice Repair
On July 15, 2010, a long section of the decorative marble lower cornice, located on the Hotel Monaco’s exterior façade, suddenly fell. An initial investigation was performed, concluding that the failure was caused by water infiltration through cracked and open mortar joints in the parapet capstone and cornice that expanded during multiple freezing-and-thawing cycles.
To aid in the selection of replacement marble and repair design decisions, samples of marble and mortar were collected and transferred to a specialized historic testing agency. In addition, petrographic analysis of the existing mortar was performed to determine the type, composition, quantity, and mixture ratio of the binder and aggregates. Upon completion of historic research, the source of the original marble was located in the nearby Beaver Dam quarry in Cockeysville, MD—providing an ideal match of materials as well as savings in cost and time.
The design and execution of the repairs to the hotel’s façade included the meticulous removal of unstable portions of the cornice. In addition to the replacement of the failed pieces, further repairs were completed, including repointing, Dutchman repairs, face patching epoxy crack injection, pinning and stabilizing of loose and/or exfoliating façade elements, and general cleaning of the marble facade within the repair area.
Project Details
CLIENT
Marx|Okubo
Location
WASHINGTON, DC
Market
Services
Square Footage
100,000
Year Completed
2011
Featured Team
Related Projects
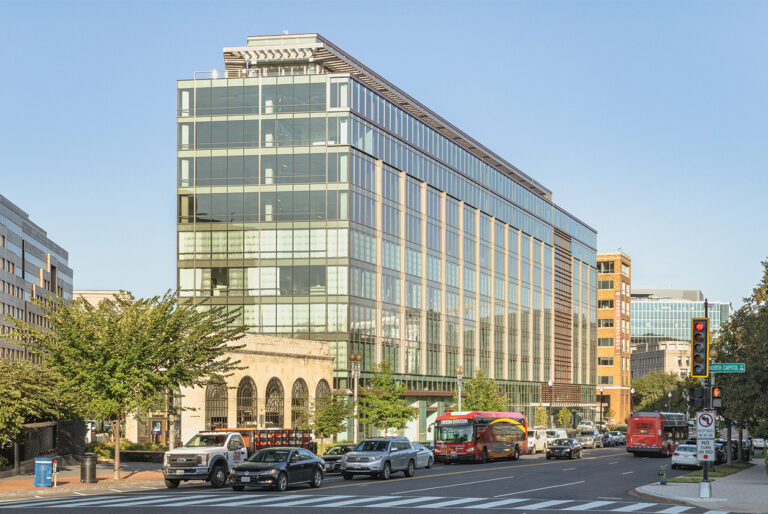
20 Mass
WASHINGTON, DC
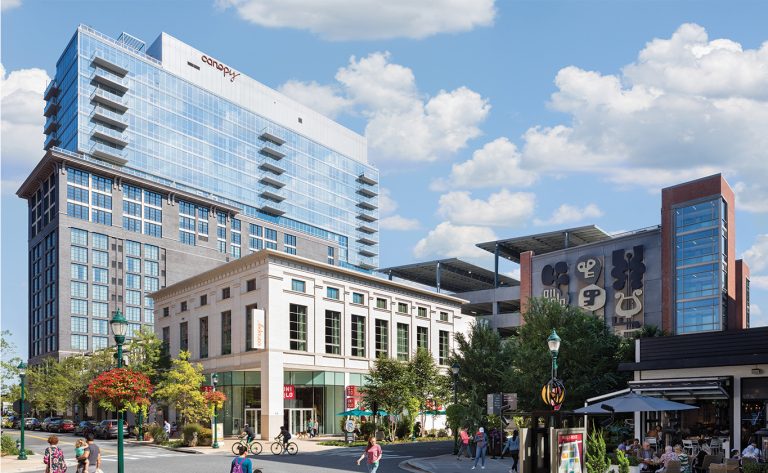
Pike & Rose
NORTH BETHESDA, MD
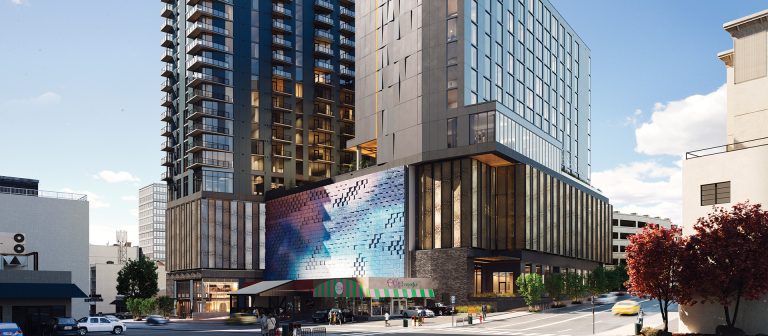
Fallyn Apartments and
Hotel Fraye
NASHVILLE, TN
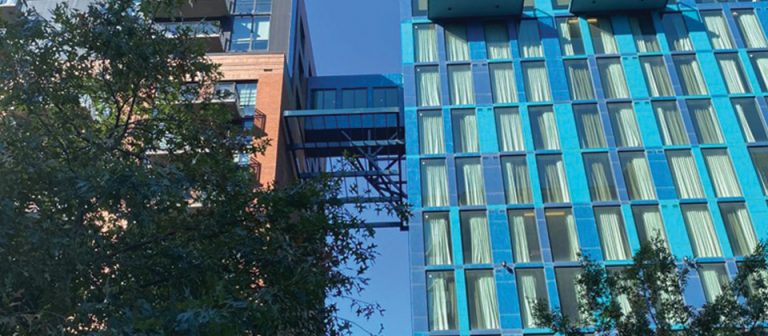
Illume CSX East
Connector Bridge
WASHINGTON, DC
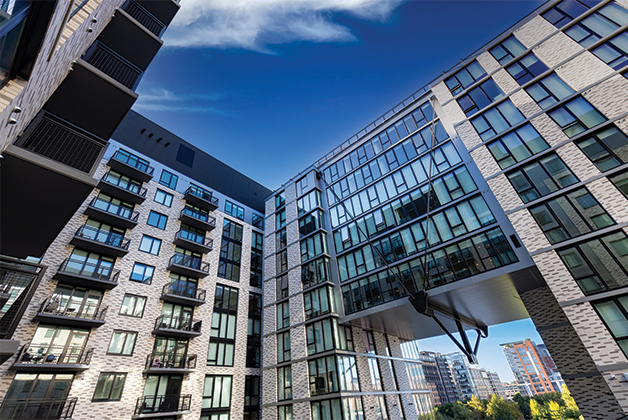
NoMaCNTR
WASHINGTON, DC
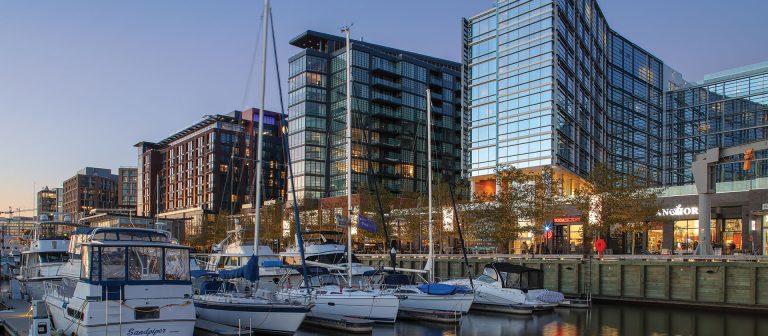
The Wharf
WASHINGTON, DC
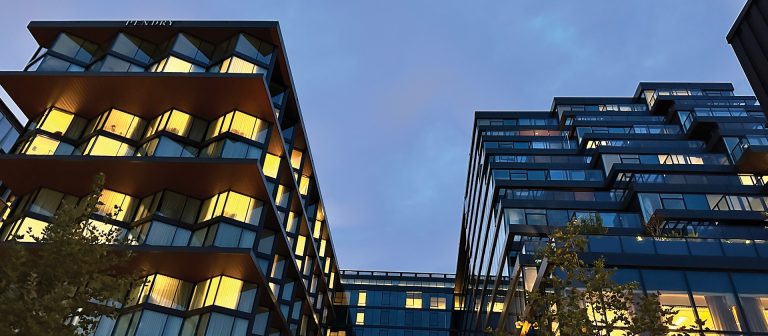
The Tides Apartments and Pendry Hotel
WASHINGTON, DC
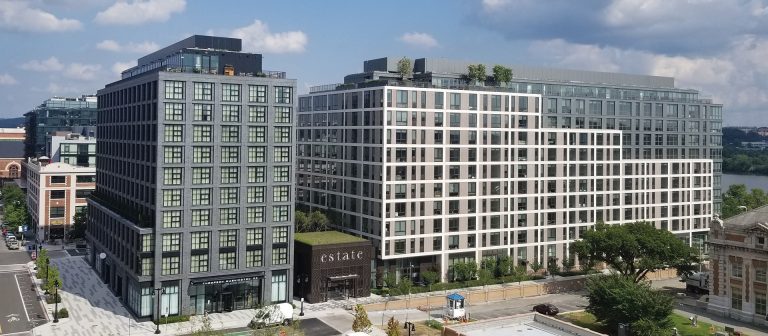
The Yards, Parcel L
WASHINGTON, DC
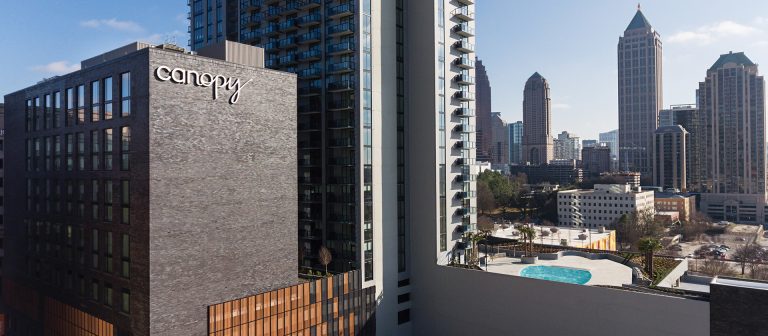
Ascent Midtown & Hilton Canopy Midtown
ATLANTA, GA